Lock and Dam #7 Gate Replacement Completed
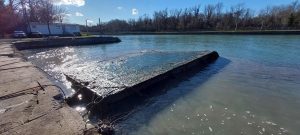
The gates are 85 feet high and 47 feet wide and weigh just under 1 million pounds each. They had been stored underwater to prevent exposure to oxygen and corrosion in a cut along the canal, not far from the ship transiting channel, with about 7 feet of water covering them, said Jose. A second set of gates was similarly stored underwater below Lock #1 near Lake Ontario, and they were floated and rolled up on air bags and into E.S. Fox’s Industrial Dock in Pt. Robinson, Ontario, on Dec. 16. Once this second set of gates is cleaned, removed of redundant equipment and attachments, blasted, inspected, reinforced, modernized and coated, the gates will either go back down to below Lock #1 to be sunk again or handed off to be installed at Lock #6 in 2026, in a similar way as E.S. Fox just did at Lock #7. This is all dependent on SLSMC tendering processes and budgets. This would be a separate work contract, Jose said.
Fabrication Process
New wall plates were also installed in the quoin areas of each lock. In previous contracts from Lock #1 to Lock #7 over the previous 10 to 12 years, these wall plates were fabricated in a concave shape and made from “Nitronic 60,” a durable and corrosion-resistant steel. The quoin and mitre ends of the 85-foot mitre gates have a new set of “bearing plates” installed on them that are a carbon steel/316 stainless steel laminate that is explosion-welded to the carbon steel underneath, said Jose, to mate the two types of steel together. The explosion-welding process, invented by Dupont in 1944, must be carried out in an abandoned coal mine in Pennsylvania. Very few companies have mastered this proprietary process, he said, adding, “The Chinese have been trying to learn it and perfect it for years.”
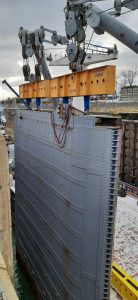
After the explosion-welding, the pieces are straightened by a massive hydraulic press into a straight uniform layer and cut into desired sizing for the end user from 4-inch-thick slabs. E.S. Fox then has each of these cut pieces machined into a final convex or flat piece down to a few thousandths of an inch for the new bearing plate, depending on if it is the quoin or mitre end of the gate.
“After setting bearing plates and alignment in numerous stages and multiple trips up and down in the dark over days, (That way we don’t have to deal with thermal growth from the sun while setting these bearing plates.) and finally, machining the pair of mitre gates to .5mm or .02 inches over 85 feet from top to bottom, we power grout behind all of the bearing plates with epoxy backing material to ensure all gaps are filled to secure and allow for compressive strength. We do all of this while maintaining 50 degrees to 70 degrees Fahrenheit in the dead of winter 24 hours per day,” Jose said.
After the first set gates were raised in the summer of 2023, they were cleaned and sand-blasted, and their fittings had to be replaced. When these gates were originally fabricated, locks used sheaves, cables and drives for moving and lifting instead of today’s new hydraulic cylinder set ups. These gates were also given new white oak timbers machined to within 1/32 of an inch, prior to floating and installation at Lock #7 the first week of January 2025.
Well-Established Business
The modern construction of the 189-mile-long St. Lawrence Seaway took place during the 1950s. Of its many locks, eight were built and are maintained by Canada and two by the United States to lift vessels 246 feet above sea level as they transit from Montreal to Lake Ontario.
Headquartered in Niagara Falls, Ontario, E.S. Fox Ltd. is Canada’s leading multi-trade fabricator and constructor. According to one business publication, E.S. Fox, in business since 1934, is the leading provider of union ironworkers’ work hours in the province of Ontario. The company erects and maintains bridges, builds nuclear power plants, and provides project management services for a variety of construction and contracting projects.
Images courtesy of E.S. Fox
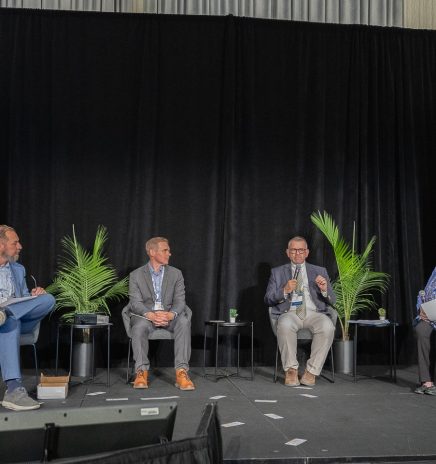
Industry Stakeholders Gather for the AGLPA 2025 Conference
Photos by Victor Studio – Chicago, Illinois The annual American Great Lakes Ports Association (AGLPA) Conference took place August 14 and 15. Industry stakeholders and leaders met for the two-day... Read More
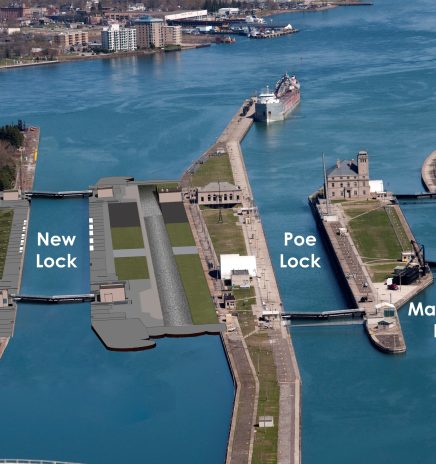
Remaining Phase 3 Options Awarded for New Lock at the Soo
U.S. Army Corps of Engineers, Detroit District’s New Lock at the Soo project in Sault Ste. Marie, Michigan, has awarded a total of $95.3 million for remaining Phase 3 options... Read More